Learn How Aluminum and Lightweight Materials are Changing Auto Body Repair
Print Article
Changing fuel economy standards and materials used in vehicle design are placing new demands on collision repair shops.
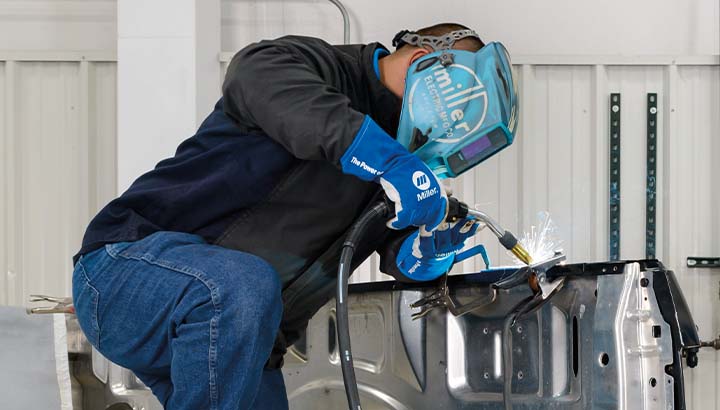
Auto body material changes
A tremendous evolution is underway in the auto collision repair industry, fueled by several factors. Increasing fuel economy standards are driving a continual move toward more lightweight, ultra-thin materials in today’s new vehicles.
As product designs change to meet these standards, automotive OEMs are using mixed-material design methods. This allows them to incorporate materials like aluminum and advanced high-strength steels in the vehicle body and superstructure. However, this places new demands on auto collision repair shops, as OEMs and insurance providers expect shops to have the tools and knowledge to fix these vehicles in accordance with new procedures and guidelines.
Choosing the right welding equipment and processes helps ensure high weld quality — from basic to advanced structural sectioning repairs. Machines with straightforward setup and adjustment controls are easier for technicians to use and help take the guesswork out of welding aluminum and other lightweight materials.
An evolving industry
While aluminum and high-strength steels are becoming more common, many collision repair shops are less familiar with welding these materials. Auto body technicians have multi-level certifications ranging from prep, painting and welding to advanced structural welding, so experience varies.
The first step toward success
Choosing the right welder and process for the job is critical to success when welding lightweight auto body materials.
Older welding equipment often doesn't provide newer technologies, like pulsed MIG welding, that help in welding aluminum or thinner materials. Some shops may have overly complicated equipment — or simply more machine than the shop needs.
The bottom line: Weld quality is a critical element in the repair of damaged vehicles. So, equipment that makes it easier to produce high-quality welds can help shops get vehicles repaired correctly to meet required safety standards — and back on the road faster for customers.
What to look for in a welder for auto repair
A simplified interface with intuitive controls allows for easily choosing proper settings and parameters. Some machines offer single knob control to adjust machine voltage and wire feed speed or automatically set proper parameters based on the wire gas combinations, wire diameter and thickness of the material being welded. This saves setup time and ensures the machine delivers the exact weld parameters needed for the job.
Having a machine capable of welding mixed materials such as aluminum or silicon bronze provides a competitive advantage for collision repair. Consider choosing a machine that also has pulsed MIG welding capabilities. Because aluminum has a much lower melting point than steel, it transfers heat away from the weld faster. This makes it more prone to burn-through and warping on thinner sections. Pulsed MIG offers a lower heat input, reducing the risk of burn-through and distortion while providing good penetration and fusion.
With the industry’s ongoing changes, the use of pulsed MIG and equipment designed for simplified use can make it easier for technicians to produce quality welds — and for repair shops to stay competitive.