Pulsed TIG welding advantages
There has been a quiet revolution in TIG welder design over the last 20 years. Virtually every machine made these days incorporates inverter technology, and that has been a game changer. This technology gives welders and welding engineers the ability to modulate the welding current in ways that were previously not possible. In particular, inverter technology has made pulsing the welding current easier to accomplish and more cost-effective, even on entry-level machines. We’ll take an in-depth look at the benefits of pulsed TIG welding in this article.
Let’s start with a definition: Pulse welding uses current that cycles between a high and low value. This has significant benefits; the most important being the ability to make a weld with good penetration but with less total heat being put into the metal being welded.

The more heat that goes into any weldment, the more chance that distortion (warping) will become a problem. This is most noticeable on thin metal sheets and on metals with relatively low heat conductivity, like stainless, and high-tech nickel alloys, like Inconel and Hastelloy. When the heat of a weld isn’t dissipated by good conductivity, it keeps the weld and the adjacent heat-affected zone at a higher temperature for a longer time, causing more distortion. Another instance where pulsing can really help is when welding out of position. Gravity always wants to pull a liquid weld downward, and if you’re welding overhead, this can be quite problematic. Pulsing helps keep the puddle attached to the metal and lessens its tendency to fall toward you as you’re welding. We’re sure you can see the benefit here!

Welding machines with pulsing capability control the highest current in the cycle — the “peak” value — and the lowest, called the “background” value. The peak setting is in amps, and the background is a percentage of peak. On the simplest machines, welders set the peak by the amperage control, and the background presets to 25% of the peak value. The frequency of the cycle is adjustable. On more sophisticated machines, you can adjust the percentage of background. Here are some hypothetical examples to illustrate the relationship between these settings. You could set the peak amperage to 100 and the background to 25, which would mean the actual background amperage would be 25 amps (25% of 100). If you kept the background setting the same but dropped the peak to 60 amps, the background amperage would then be fifteen amps (25% of 60).

On machines with more sophisticated features, you can control the percentage of time spent in both portions of the cycle.

Choosing settings
So, with all this adjustability at your fingertips, what effect does each variable have on the characteristics of the weld? And how do you know what settings to choose?
While pulsing at any frequency will lessen the total heat input, there are distinct characteristics available at different points in the spectrum. Some people use a very low pulse frequency (around one pulse per second) to time the addition of filler rod. This is similar to a musician using a metronome to keep accurate time with the music. Most welders hold the torch stationary and add filler rod during the peak portion of the cycle, then retract the rod and advance the torch during the background period. This is also an excellent way to accentuate the “dime on dime” look that many people prize as the hallmark of a beautiful TIG weld.

This low frequency may also be beneficial when making a pass over a weld that has an uneven bead profile. The slow, even pulsing can add a regular ripple pattern that wasn’t there previously. Filler rod is not generally added when using this technique.

In the two-to 10-pulses-per-second range, the arc is considered “soft.” This is ideal for you want a broad bead, and deep penetration is not the goal. An outside corner joint is one example where this may be desirable, or a final “wash” pass that caps off multiple root passes.

Pulsing between 10 and 30 cycles per second causes a “strobe” condition that many people find upsetting. You may want to experiment with this range, but you may find it disorienting. One hundred cycles per second is the default setting for many TIG welding power sources. It is a middle-of-the-road option, making it a good choice for a broad range of welding projects. It’s probably a good place to start as you experiment with different pulse settings.
Pulse frequencies above 100 cycles per second tend to make the arc “stiffer" when TIG welding. This can help drive the penetration deeper into a narrow joint. This may also allow faster travel speeds and give the arc better directional control. Some industrial-level machines provide pulsing up to 500 cycles per second, which can maximize these benefits.

The background setting allows you to control the cooler portion of the cycle. A good place to start is 25% to 40%, with higher settings giving you a more fluid puddle and faster travel speeds and lower settings giving the most reduction in the heat input.
On machines that allow you to control the amount of time in peak, a larger percentage will give you more heat in the weld, along with a wider bead and deeper penetration. Note that there can be too much of a good thing here, since the primary benefit of pulsing is to LOWER the heat in the base metal. A good place to start is between 40% and 60%.
You will need to set the amperage higher when pulsing, since the nature of the process reduces the overall heat that enters the metal.
Each welder will learn which settings work best for them in various situations. It’s good to experiment and learn which aspects pulsed TIG welding can benefit the type of work you do. You may be surprised at how many ways pulsing can ease your welding tasks.
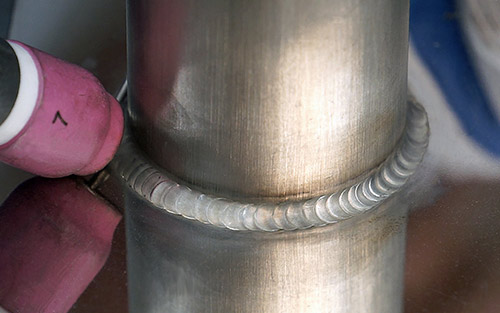