Executive Summary
Cleaver-Brooks suffered endless hours of frustration with its MIG welding system when it failed to produce continuous tack welds without excessive spatter or burn back. By switching to Miller’s Dimension NT 450, the company eliminated those problems and increased productivity through reduced downtime:
- Increased operator efficiency while reducing frustration.
- Reduced weld costs associated with removing spatter and frequent gun nozzle cleaning – as much as $20,000 in labor/year.
- ROI of 169 percent with payback in 7 months.
- Dimension NT 450 provides faster response, more positive arcs and superior arc performance.
Boilermakers No Longer Steaming: Hybrid Technology Eliminates Frustration, Saves Downtime
The challenges of maintaining a high degree of product quality while still delivering required throughput had become a real challenge for four welders on one of Cleaver-Brooks' commercial boiler lines at its Stratford, Ontario, facility.
The Model 4 and Model 5 watertube boilers they fabricate require a combination of Stick and MIG welds. The Stick welding capabilities of their multi-process welders were adequate for the job, as were the MIG capabilities, at least on the longer welds. But when it came to tack welds, the story was different.
It was difficult performing two successful tack welds in a row, and, considering that each unit requires hundreds of tack welds, hours could be lost each week to fighting the problem. Although that lost time might translate into $20,000 a year in lost time, for the men on the line there was a more immediate issue.
"The frustration level was unbelievable," says Kevin Brown, one of the fabricators on the line. "The arc would sputter, create spatter and burn back into the tip. You'd have to take the tip out, knock the wire out and put it back together. If it was bad enough, you'd have to replace the tip."
Then, in the fall of 2005, they replaced their traditional power sources with the newly introduced Miller Dimension NT 450 multi-process power sources. The Dimension NT 450 uses a hybrid technology that bridges the gap between an inverter and a traditional welder and offers true multi-process capability. Welding equally well in all processes, the Dimension NT 450 eliminated—overnight—the sputtering and spatter problems that frustrated Brown and his three coworkers on the watertube line.
A watertube boiler, as the name implies, feeds water through tubes of the boiler, while heated combustion gasses on the outside of the tube make multiple passes to heat the water. They tend to be relatively small, taking up minimal floor space. The Model 4 and Model 5 are top of the line commercial/small industrial boilers designed to fit through a standard doorway, eliminating the need to knock out walls for installation.
 |
Fig. 1: A Cleaver-Brooks Model 4 watertube boiler in the making. Four rows of 30 tubes are first Stick welded top and bottom and then joined by membranes.
|
By comparison, firetube boilers pass combustion gases through tubes that are surrounded by water. Cleaver-Brooks manufactures both types and is one of the leading manufacturers of commercial and industrial packaged boilers and systems used for heating and steam processes.
With headquarters in Milwaukee, Wis., and seven factories throughout North America, Cleaver-Brooks (http://www.cleaver-brooks.com/) developed the packaged boiler 75 years ago, and as its charter, committed to being a technology leader then, and is still in the forefront of the industry today. A packaged boiler includes the boiler/burner and all of the wiring, safety and control features, requiring only hookup to gas and electricity to be ready to go.
Boiler vessel designs don't change often, according to Craig Schlemmer, manufacturing manager, Cleaver-Brooks, Stratford, Ontario. The greatest advances have been in the electronic control systems and burner designs.
"What we put on boilers today-PLCs, low emission burners, variable speed drives- is far different from what we did 10 years ago," says Schlemmer. Among the benefits of modern control technology is enabling remote monitoring of boiler systems.
The Stratford plant manufactures firetube packages, deaereators (which remove oxygen from the boiler feedwater, increasing longevity of the boiler) and commercial watertubes. Of its 88 hourly employees, 28 are certified welders—ASME section 1(high pressure), section 4 (hot water boilers) and section 8 (tank vessels). All of the material used is approved by the ASME (American Society of Mechanical Engineers) and an inspector from Technical Standards and Safety Authority (TSSA) is on hand to inspect every vessel.
Four welders, two per shift, work on the watertube line. Model 4 and Model 5 differ only slightly to meet country-specific requirements. Model 5 is for Canadian distribution only.
These models feature approximately four rows of 30 water tubes (Fig. 1) of .095-in. wall carbon steel Stick welded at top and bottom. Membranes (1-in. wide strips of 12-gauge steel) are MIG welded between them, forming a chamber in which hot gases make multiple passes before exiting through the stack, which is made of 20-gauge steel.
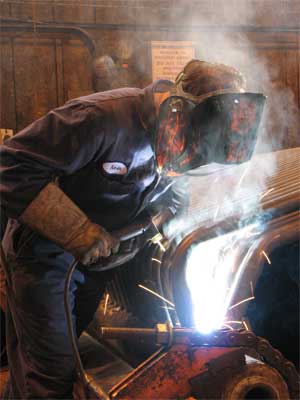 |
The operators use Hobart Brothers 6013 (5/32-in.) and 6011 (3/16- and 1/8-in.) electrodes, which they bend to get into hard-to-weld positions.
|
"There's a ton of welding on these units," says Mike Ruston, fabrication supervisor. "It's an art form all by itself to weld those tubes in place."
For years, separate MIG and Stick welders were used on the Model 4/5 line, but three years ago they were replaced with multi-process power sources in an effort to update equipment.
"Stick welding was fine," according to Al Bungay, a fabricator with 18 years of welding experience. "So was the MIG arc, once you had it going, but there was a problem with the tacking. Often the arc would sputter and you'd get burned, for one thing. Then there was a lot of time involved in removing spatter."
Each of the membranes requires about a dozen tack welds. The fabricator starts at the top, tacking the 12-gauge steel into place, and then forms it to conform to the pipes, tacking it as he goes (Fig. 2) Then they are welded to create an airtight seal. The stack, with its light-gauge steel, requires 100- 200 tacks.
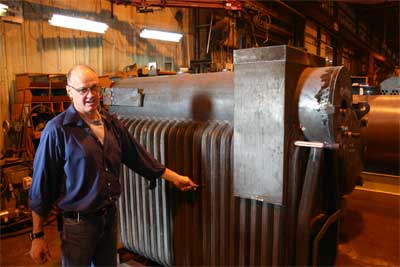 |
Mike Ruston, Cleaver-Brooks fabrication supervisor, points to the membranes on a Model 4 watertube boiler. Tacking the membranes into place was costing the company in time and frustration. (inset IMG-0445). The stack, shown here, also requires numerous tack welds on thin gauge material.
|
"You could spend 15 minutes a side chipping spatter," says Bungay. "About five times per side you'd have to take the tip off and clean or replace it. Tacking problems could eat up 45 minutes to an hour per day per person."
With four people experiencing the same issue, non-productive time could amount to three to four hours a day or 15 to 20 hours per week. Assuming an average wage of $20 an hour, that could amount to $15,000 to $20,000 a year.
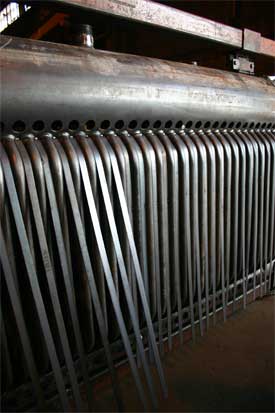 |
Fig. 2: The metal for the membranes are first tacked in at the top and then formed along the contours of the pipes. Numerous tacks are required to hold the membranes before final welding. Since acquiring Miller Dimension NT 450s, frustration level is down and productivity is high.
|
However, it wasn't even the monetary aspect that was the greatest concern to those in management and on the line. Rather, it was the frustration caused by the individuals' pride in workmanship, and Cleaver Brooks' ongoing commitment to maintain the highest quality standards in the boiler industry while respecting their commitment to on-time delivery.
"When they were tacking, the gun would sputter, sending sparks down their necks," said Ruston. "They'd hit the boiler with the gun and would have to clean the tip. Then they'd try it again and it might sputter or it might work for six tacks in row and then act up again."
"You'd be very frustrated by the end of the day," says Brown.
Experts were brought in to fine-tune the machines, but nothing helped the tacking issue.
"Usually if you have spatter, it means there's something wrong with the settings, but the machines couldn't be dialed in," says Bungay. "They figured we were the problem. They seemed to think that we didn't know what we were doing, and I've been welding boilers for 32 years."
For help Ruston turned to Mike Conners his local Praxair representative, who contacted Dave Middlebrook from Miller Electric. Middlebrook explained that a traditional multi-process power source is "hard wired" to give acceptable performance in all processes; however, designed to provide all processes, it doesn't excel in any one. The existing machines just weren't able to perform repetitive tacking well.
Middlebrook suggested they try the Miller Dimension NT 450 multi-process power source, which had recently been introduced. The Dimension NT 450 features a new hybrid technology that combines the performance of an inverter with the reliability of Miller's transformer-based Dimension family.
While an SCR based power source is limited by the frequency of the input power, the Dimension NT 450's fast switching technology provides a much higher operating frequency, allowing faster response, more positive arc starts and superior arc performance in all processes. Advanced control circuitry optimizes the arc for each welding process. Designed for heavy industrial applications where the lightweight portability of an inverter is not required, the Dimension NT 450 provides 450A at 38VDC, 100-percent duty cycle. The faster response time and superior performance solved the problems.
"Dave gave us a Dimension NT 450 demo model to try," says Ruston. "We liked it so much, we didn't give it back. Then we bought another one. It's a night and day difference."
Using the same wire feeders as before, Miller 60 and 70 series running .035-in sold wire, the tacking problems and the complaints went away overnight.
"The Dimension NT 450 is an excellent machine," Bungay says. "The starts are excellent. It's made our job a lot easier, probably taking a day out of the process. The greatest thing is far fewer interruptions. I can whip down a whole side and only have to clean the tip once. This is a big-time improvement."
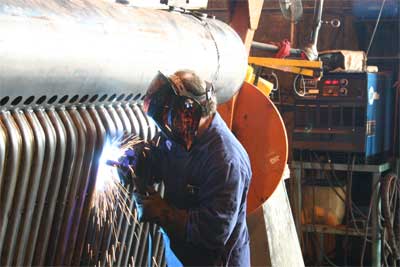 |
Al Bungay can now weld the membranes into place in a fraction of the time it used to take without sacrificing quality.
|
Brown agrees with his assessment, saying, "These welders are unbelievable in the time they save and in the quality of the welds. They run really well at the low settings, like those we use on the stack where we're welding 20-gauge material. We were so frustrated before that we wanted to take a hammer to the MIG guns. That's over."
The Dimension NT 450 brought another, unexpected benefit: improved Stick performance. Even though Stick performance was fine on the previous units, the Dimension NT 450s, with their enhanced Stick starting capabilities, gives the operators more positive starts.
"We used to have to hit the welding rod," Bungay says. "Now it just starts going right away."
Even without savings that could amount to $20,000 a year and tips that last three times as long, Ruston is satisfied with his purchase.
"Just from a reduced operator frustration level, the Dimension NT 450 was a good investment," Ruston says.
