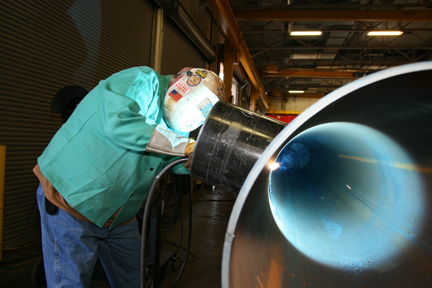
As production and engineering managers for Bel-Aire Mechanical, Inc., of Phoenix, Ariz., Mike Mackintosh and Darwin Terpstra faced the same challenge as do most pipe fabrication supervisors: producing the highest quality product in the shortest amount of time, with minimal rework and using a labor force of varying skill levels.
And, as with others in their position, they sought to overcome the limitations of the Stick process—such as its relatively slow travel speed—by using MIG, which is faster and easier to train. Unfortunately, standard MIG isn’t ideally suited for pipe welding; its higher travel speed can be offset by the clean up time required and a 10-percent or higher rework rate.
Plus, as in other pipe fabrication shops, Mackintosh brings in additional welders when the workload demands it, creating a work force with a diverse range of skill levels and operator styles. Each weld could look as unique as the welder’s signature.
These challenges are not unique to Bel-Aire—all pipe fabricators must face them—and Bel-Aire had done well, growing to be one of the top mechanical contractors in the state. Then, in 2006, Bel-Aire purchased a new building and Mackintosh and Terpstra took the opportunity to recreate the pipe welding operation. In addition to examining the workflow through the pipe shop and eliminating bottlenecks, they took a close look at the MIG and Stick processes they had been using. Once they saw the technologies and equipment that were available, they mothballed the existing welding equipment. In its place, they brought in welding systems that use the modified short circuit process, RMD™ for the root pass and ProPulse™, an advanced pulsed spray transfer process for the fill and cap.
The result: Bel-Aire doubled production—three welders now do what it used to take six welders to accomplish. Plus, the welders now produce uniform and nearly identical welds. Bel-Aire now performs two distinctly different welding processes using the same welding machine, the same gas, and the same wire for the root, fill and cap passes, reducing inventory of wires, gasses, and other consumables. This has shortened training times and has eliminated weld rework all equating to cost savings.
“Previous rework rates could be as much as10 percent, depending on the application and testing parameters,” says Mackintosh. “Now, rework is no longer a factor.”
Bel-Aire Gets Its Start
Co-founders James Dinan and John Sapien founded Bel-Aire in 1986 after recognizing a need for a mechanical contractor to provide both solid HVAC capabilities and primary contractor related services. The company started off with the smaller jobs, and today, with over 300 employees, Bel-Aire is actively involved in mechanical construction, renovations, upgrades and remodels in the valley and throughout Arizona. Its projects range from multi-million dollar mission critical facilities to turn-key, fast track retrofits.
It leads the field in many areas, including Building Information Modeling (BIM), which allows Bel-Aire’s design department to create a virtual fly-through to ensure there are no collisions with piping, plumbing, electrical, sheet metal and fire protection systems. Bel- Aire works with architects, engineers and other contractors within a collaborative environment to provide a coordinated, collision free model prior to fabrication.
 |
Bel-Aire’s state-of-the-art Building Information Modeling (BIM) programs allows them to fly-through a 3D model to ensure there are no conflicts. |
Opportunity Knocks
“When Bel-Aire purchased its new facility, we were provided a great opportunity,” Mackintosh says. "We were able to start over from the beginning. We had time, because the building wasn’t quite ready for us to move into yet, and I had tremendous amount of support from Jim Dinan, our CEO and John Sapien, our Chairman. We took the opportunity to look at the entire workflow.”
Some of the changes Mackintosh and Terpstra implemented included the addition of a computerized pipe cutter, which, in a few hours, allows one operator to equal the work previously done by two in eight hours.
 |
As part of the overhaul of its pipe fabrication shop, Bel Aire added a computerized pipe cutter to streamline the process and ensure that the pipes are properly prepared. |
“That was a tremendous change,” Mackintosh says. “We looked at everything needed to make a high quality weld. We added a bead blaster to ensure that pipe and fittings were free of paint and other contamination. We made sure we had the proper bevels. The best welder in the world will not overcome poor preparation.”
One of the most significant changes came when Mackintosh replaced the existing Stick and standard MIG equipment with equipment that offered RMD™ (Regulated Metal Deposition), a modified short circuit MIG process optimized for root pass welding, and ProPulse™, an advanced pulsed MIG process optimized for the fill and cap passes. These would change the nature of Bel-Aire’s welding operations.
Out with the Old
Bel-Aire works in accordance ASME Section 9. Prior to adopting the new processes, the company had been using Stick, primarily 6010 electrodes, and standard MIG processes. To get the advantages MIG promised in other applications, such as increased travel speed and less operator training compared to Stick, Bel-Aire had acquired four 300-amp MIG welders.
“The MIG equipment worked fine,” Mackintosh says. “I’m sure they have their place, but not in the pipe world. The weld time was quicker than Stick, but the time required to clean between passes offset those savings. With MIG, we would occasionally have lack of fusion, or inclusions which could lead to leaks.”
Mackintosh adds, “If you’re not skilled with standard short circuit MIG, the tendency is to trap inclusions or get porosity in the weld. Then you have to remove it, grind it until you have good material and start over again. That’s costly and time consuming.” Including the time to discuss the issue with the inspector, reload the pipe into the positioner, grind down to good metal and reweld, reworking a weld could cost twice that of the original weld.
“With Stick or MIG, if you put three welders under the hood, you’ll have three completely different looking welds,” says Mackintosh. “They would all be acceptable, but you could tell which welder was more experienced.”
The issue, of course, wasn’t with the operators. They are skilled, trained welders. Nor was it with the equipment, which worked as well as the day it was manufactured. The issue was that the welding equipment and processes were not designed for pipe welding.
In with the New
The welding equipment Mackintosh brought in was specifically optimized for pipe welding, featuring RMD™ for the root pass and ProPulse™ for the fill and cap passes.
RMD is a modified short circuit transfer process that precisely controls welding current during all phases of metal transfer to eliminate excess weld puddle agitation. This results in a calm weld puddle that is easier for the operator to manipulate and eliminates cold lap, which occurs when molten metal splashes against the side wall of the pipe and “freezes” on top if it. RMD™ is highly tolerant of high-low misalignment because it has a faster freezing puddle that stays where it’s put.
Pro-Pulse™ technology is an advanced pulsed MIG process that controls both current and voltage to stay within the optimum range for a specific wire type and diameter, wire feed speed, and gas combination. Optimized specifically for pipe welding, ProPulse™ provides a much cooler weld puddle that is ideal for out-of-position welds. While the details are transparent to the user, who only needs to adjust a few settings, the result is shorter arc lengths and a more focused arc column. This provides a weld puddle that is easier to control. Operators learn the process faster and make higher quality welds with lower reject rates. The process also is more tolerant of contact tip-to-work-distance variation, provides improved fusion and fill at the toes of the weld, which helps ensure quality welds are achieved on the first try and has a lower overall heat input, which reduces interpass cooling time and weld cycle time. Mackintosh immediately saw the benefits.
 |
The RMD and ProPulse processes have decreased training, ensured uniformity and eliminated rework. Both processes are very tolerant of wire stickout and are much more forgiving than Stick or standard MIG processes.
|
“One of the first things I noticed, is that welders don’t have to be as highly skilled,” Mackintosh says. “After three or four hours of coaching, a less-skilled operator would be consistently producing high quality welds. When the work load increases and we bring in new welders, I now can feel comfortable that the time to get up to speed will be short.”
Because Stick and MIG require more training and skill than the new processes, the operators’ skill levels were evident in the welds. But the new processes, being very tolerant of differences in stickout, changed that.
“Now, it’s hard to tell one welder from another,” Mackintosh says. “The new technologies level the playing field between our less and more experienced welders. Customers think we’ve fully automated the process because the welds look uniform and identical, and I have a huge amount of confidence in every weld we make.”
With both process in one machine, using the same gas and wire, it eliminates the need to have separate machines, wires or welding processes for root and fill passes. Operators only need to push a switch between processes and utilize the pre-programmed parameters. One of the things Mackintosh has to teach experienced MIG welders is to not try adjusting the parameters. “We use the same RMD program on two-inch pipe as we do on 24-inch pipe, and we use two programs for ProPulse, depending on the configuration,” Mackintosh says. “I can assure our customers that each welder is using the same wire feed speed, and voltage, and that all of the welds we make are of the same quality, and we’ll have the same high quality for chilled water pipe as we do on process piping.”
 |
Welders can switch between the modified short-circuit process and the advanced pulsed MIG process with a push of a button. Using one welder, one gas and one wire has eliminated the need for multiple machines in a welding cell. |
The new processes eliminate cold lap, inclusions and the other issues associated with using standard MIG for pipe welding.
“Rework is now almost nonexistent,” says Mackintosh. “People are going to look at that and ask, ‘Is it possible?’ but it’s true. I can now put an estimate together and not have to consider rework in the equation. Rework due to weld quality is no longer a factor.”
As mentioned, rework time could be double that of the original weld. That time is not figured into the increased productivity, which, Mackintosh estimates, has doubled by refining the pipe preparation and using the new welding processes.
“With three welders welding all day long, I’m saving about 60 hours a week,” he says. “On a six-inch joint, time has decreased by 50% and we’re using half as many machines to do twice as much work.”
Perhaps the only drawback that Mackintosh found is that RMD and ProPulse look the same as standard MIG.
“Customers will notice the gun and the roll of wire and the first thing that would pop into their minds is ‘Why don’t you use Stick?’” Mackintosh says. “Especially on the process piping. But this is nothing like MIG. It’s really a different process, and once the customers see what it can do, it’s easy to sell.”
 |
 |
Nick Peterson, Miller Electric Mfg. Co., and John Maloney, of Bel-Aire Mechanical discuss setting up RMD and ProPulse programs. |
Darwin Terpstra, project and engineering director and Mike Mackintosh, production and design manager, Bel Aire Mechanical, in the streamline pipe fabrication shop. The purchase of a new building allowed the company to retool its welding operation from the ground up, with an eye toward boosting productivity.
|